The behavior of entrapped air in the mold is often unclear. Unsuspected air entrapments appear and have negative influence on the part quality. Their real position, shape and consequences usually become visible in the finished part only.
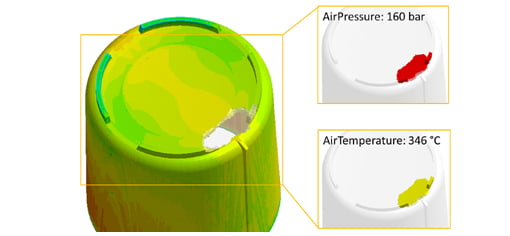
With the process oriented simulation of SIigmasoft® they can be reliably predicted from the beginning of the part and mold development. The once more enhanced venting option allows to compare different venting solutions and to evaluate their efficiency based on physical factors for plastic, thermoset, elastomeric and MIM/CIM applications.
To be discovered in Singen At [wfb] show from June 19th to 20th in Siegen, Germany, the Sigma Engineering GmbH from Aachen, Germany, presents at booth S06.04/05 how simulation can help to make the behavior of air in the mold physically transparent and thus to recognize air entrapments and resulting defects early and to specifically avoid them. Entrapped air and its position in the part have a huge influence on the quality of injection molded parts.
To avoid bad quality Negative effects are numerous: Besides problems during filling and mechanical weak spots caused by air bubbles inside the part, they are a main reason for visible streaks and burn marks on the surface for plastics; for elastomers and thermosets the high temperature of the entrapped air starts an early cross-linking reaction, which leads to further part defects; in applications with complex inserts entrapped air corrupts the adhesion between polymer and insert or leads to part defects as soon as they come loose from the insert and are transported into other regions by the melt. Usually the exact position and size of air entrapments cannot be determined until the first parts are produced and corrections are only possible over subsequent constructional changes on the mold.
To save time and money The process simulation with Sigmasoft® makes it possible to give an accurate prediction of entrapped air and air bubbles as well as of their movement through the melt in critical regions of the part before the mold is built. Thus it allows an evaluation of their consequences for the part quality. Counter-actions can be taken early in the development process and at low costs. However process simulation is also beneficial for existing production processes. It is an adequate tool to detect the real cause for burn marks or other defects. Vague presumptions are replaced by clear facts.
To help design efficiently Additionally to the determination of possible air entrapments and their consequences Sigmasoft® offers the possibility to validate the positioning of venting and its efficiency thanks to the integrated advanced venting option. Possible solutions to avoid defects can be compared in short time before changes are made to the process or mold. The influence of venting on the filling behavior is immediately visible in the simulation and in the result interpretation possible burn marks or other defects can be clearly identified.
SIGMA Engineering GmbH i. A. B.Sc. Vanessa Schwittay Engineering, Marketing Tel. +49 - (0)241 - 89495 - 23 Fax +49 - (0)241 - 89495 - 20
[email protected] www.sigmasoft.de
.
.