Producing highest quality watch cases is RM Lifestyle’s passion. Renowned manufacturers of top-of-the-range watches such as JS Watch expect this quality. RM Lifestyle has thus acquired an automated and customised engraving and marking system for engraving cases bottoms according to customer wishes. The company has thus gained independence from external suppliers and gained process stability and flexibility for itself and its customers.
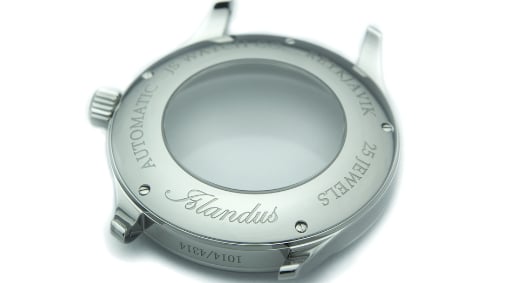
JS Watch watches are highly appreciated by connoisseurs from all over the world who love the quality and exclusivity of the small Icelandic watchmaking workshop. Chronometers in particular attract more and more amateurs thanks to their uncompromising design and technology, which is ensured by master-watchmaker Gilbert O. Guðjónsson and his son Sigurður Björn, at the head of JS Watch. The watches are assembled by hand with great attention to detail in the centre of Reykjavik with a handful of employees. JS Watch expects the same enthusiasm for the product from its carefully selected suppliers who deliver components such as movements, pointers and cases. In RM Lifestyle based in Pforzheim, the city of jewellery and watchmaking, the artisans from Reykjavik have found a committed and capable partner. Founded in late 2014, the company has successfully dedicated itself to the production of high quality watch cases with lot size starting from 25 units. RM Lifestyle has laid the foundations for its rise in this demanding activity by purchasing an automated watch engraving plant, of which the LASERPLUSS RayDesk device is the centrepiece.
Increased added value through laser marking "What we need is a precise, uniform and distinctive engraving that can still be read easily even after many years", explains Rolf Koch, Managing Director and co-owner of RM Lifestyle GmbH, listing the quality features that an engraving must fulfil. In the past, his company subcontracted the engraving work to Swiss specialists, who offered their services on the basis of traditional processes such as mechanical engraving with a chisel or chemical engraving with acids. "We had finally encountered problems of quality and deadlines. So we decided to take over the engraving process ourselves so that we could control the entire value chain internally, from the bar material to the finished watch case, including engraving," explains Rolf Koch.
Laser technology was quickly identified as a possible solution. It offers a quality comparable to that of conventional processes, but has a number of obvious advantages: it requires no jig ,no tools subject to wear or high clamping forces and is faster and cleaner than conventional engraving.
Laserpluss wins the contract Rolf Koch returns to the evaluation phase. " It quickly became clear that only a few laser system suppliers were able to meet our high requirements for engraving quality and degree of automation". Four candidates were then pre-selected. The choice was finally made after an engraving test. The idea was to mark a ring-shaped watch case back on a strongly rounded edge (a 90° arc of a circle) with a micro-engraving. "One important supplier didn’t even take up the challenge. A second was able to present a very interesting concept but was ultimately unable to solve the task". Among the two remaining candidates, Laserpluss clearly won the race.
High level of automation for optimum results "These results are due in particular to the automated handling of the parts (ring manipulation), with which the RayDesk can be supplied as an option and which always returns the watch to the optimal position with respect to the laser beam. The unfortunate finalist had a pallet handling system to automate the machining process, but manual ring handling," explains Rolf Koch. After LASERPLUSS had also accepted overall responsibility for the automation of the entire system, from automated part insertion to the cleaning unit, RM Lifestyle placed the order with the Idar-Oberstein laser processing specialist and has not regretted it for a second to date.
Designed for operation withour dedicated staff The system, which went into operation in spring 2016, has been designed for 24-hour automated operation and includes, in addition to the RayDesk with 3-axis ring handling system and camera, a robot with articulated arm, four pallet slots and further functinal modules. The robot removes the workpiece from the pallet with a specially adapted gripper and places it under the camera. "The camera system, integrated in a housing with special lighting, is deliberately placed outside the RayDesk, which means that the time required for measurement is not taken during the cycle, but only during non-productive processing times," explains Rüdiger Emrich, who initiated and coordinated the project at Laserpluss
Once the camera has determined the orientation of the workpiece using existing holes in the workpiece, the robot inserts the it into the RayDesk. Based on the alignment, RayDesk calculates the individual starting point for engraving so that the laser can begin processing quickly and with absolute accuracy immediately after the background is inserted into the handling system.
Customer specificities that have proved their worth "The entire system consists largely of components that have already been tested in other applications such as the RayDesk, robot or external camera as well as our operating software, which we have extended to customer-specific components," explains Rüdiger Emrich, area sales manager at Laserpluss. We have ensured maximum integration so that the user can program the robot via RayDesk software, for example." "Laserpluss has perfected the system so that we can exert influence exactly where we want, the software does the rest," confirms Christian Gammel, system operation and programming manager at RM Lifestyle.
Engraving and cutting: from a single piece to series production The system is so flexible that ring operation can be switched off in a few simple steps, for example, to load the RayDesk directly with entire pallets, the integrated camera of the laser marking system also taking over the task of the external camera in this operating mode. It is also possible to load the system manually to quickly perform individual parts or machining tests. The laser source is also so powerful that it can be used for cutting thin metal sheets.
"The fineness and quality of the engraving as well as the great flexibility and performance of the Laserpluss system make us independent of external service providers", summarises Rolf Koch with satisfaction. "It also allows us to enter new business sectors such as contract engraving or the manufacture of industrial products".