Laser sintering technology enables medical technology designers to print plastic objects for feasibility studies within a very short time. The functional prototypes largely have the same properties as injection-moulded parts. EEM AG goes one step further: It manages a balancing act between the production of prototypes and small series.
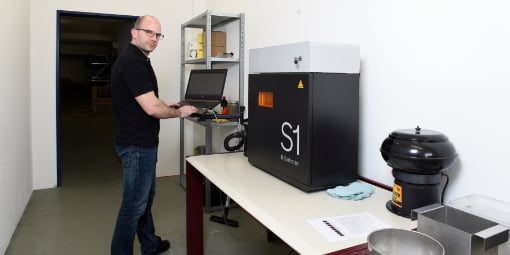
‘The spine is the key to health’ - Cyrill Aemisegger, responsible for development, technology and production at EEM AG, reminds us of this 2000-year old quote by Hippocrates: ‘That’s where we start.’ The young company manufactures various health-promoting products under the ‘grow concept’ brand that enhance well-being and performance at home, in therapy or at work. In addition to a sound system with soothing music and relaxing, scented aromas, EEM’s flagship is its developed and patented special chair, which – using an innovative process – relaxes the back within 10 to 20 minutes.
Special chairs for extension therapy It’s evident that this is like selling water in the desert. Back pain is one of the most important causes of inability to work. In Germany, for example, nearly one in three adults has back complaints often or constantly. In total, these conditions are responsible for around a quarter of all sick leaves. However, the number of unreported cases is high, and other ailments can also be caused by an unhealthy posture. These may include eye complaints, arthritis, foot pain or sleeping disorders.
One remedy is the so-called extension therapy, which takes place on specifically developed and automatically adjustable relief chairs. We are in the EEM showroom in a small village in the canton of Thurgau surrounded by green pastures, old apple trees and vineyards – a place where you don’t exactly think about back pain. Cyrill Aemisegger explains: ‘Instead of taking painkillers, the grow chairs tackle the health problem at its roots.’
Daily strain causes our spines to shrink by up to three centimetres in the course of the day, depending on physical activity. The treatment on the grow chair ensures that the spine expands again - with positive side effects that promote the body’s regeneration: The nerves are calmed down and stress is reduced. ‘It makes a short break feel like a brief holiday,’ says Cyrill Aemisegger. And the feedback he receives is extremely positive: Several hundred grow chairs have already proven themselves in use.
More than 20 printed parts per chair In order to be able to produce components with any geometry as directly as possible, EEM has been using selective laser sintering (SLS) technology since the development of the three grow chair models began. A total of more than 20 functional objects per relief chair is now produced using the 3D printing process. The chairs are still at an advanced prototype stage. However, in the models produced to date, the 3D-printed components do not serve as placeholders for injection-moulded parts for the future mass production, but are fully functional. They have largely the same mechanical and visual properties. Combined with the ability to quickly change printed partial-geometries, the process is proving to be the most efficient production variant for current small batch production. The company from eastern Switzerland thus manages a balancing act between prototyping and small series production.
In addition to 16 mobile protective covers, the electronic protective socket, the holder for the remote control and the clever quick-release system for the exchangeable headrest are laser-sintered. Distinctive: The holder for the remote control is a design element with a modern look and feel that is strongly in the foreground.
FFF and SLA did not meet the requirements Cyrill Aemisegger, a trained polymechanic, is perfectly versed in conventional production methods. Since, for example, he could not find any usable standard parts for the electronic cover, he decided to manufacture certain components himself. He did not consider CNC milling for these special components, due to its limited agility. In 2017, he then looked for an efficient solution that would be best suited for manufacturing these parts.
When Cyrill Aemisegger studied the various 3D printing techniques in more detail, he noticed that he had high demands. For him, FFF (Fused Filament Fabrication) technology was out of the question due to the support structures (also known as FDM: Fused Deposition Modelling). The development manager explains: ‘The post-processing involved would have been too costly for me.’ Even the SLA process (stereolithography) did not meet his requirements. This was especially the case because parts printed in this way would not be mechanically stable enough and would have to be reworked at great expense. And because a high-end SLS system is simply too expensive for a small business like EEM, he quickly came across the affordable ‘Sintratec S1’.
If Cyrill Aemisegger had outsourced the aforementioned plastic parts as injection moulding orders, production would not only have been much costlier, but also a lot more time-consuming. ‘Thanks to SLS technology, we achieve immediate results and can thus accelerate our development processes,’ says the technology manager.
Exemplary essence of SLS Selective laser sintering offers designers and engineers fascinating ‘process-specific’ possibilities that allow for completely new designs. An example of this is the quick-release system of the headrest, which impresses with its small but subtle ingenuity: The design of the two moveable parts printed inside each other would not be possible with either a conventional manufacturing system or any other affordable 3D printing system. The advantage of this design: With the mounted spring, the locking function is also elegantly provided. ‘Thanks to SLS technology, we can implement more complex designs and build them precisely for their function,’ continues Cyrill Aemisegger.
The use of the Sintratec S1 has had a significant impact on EEM’s engineering. ‘Since using the Sintratec S1, we have been designing in a much more function-oriented way’ sums up Cyrill Aemisegger. ‘The Sintratec S1 is used day and night in our production and it is hard to imagine working without it.’