Harder, sharper and cheaper test probes for PCBs will be the result of a new coating developed by Swedish company Impact Coatings. The alloy, Ultra MaxPhase™, has a Vickers hardness specification exceeding 1600HV, harder than rhodium (600-1000HV) and much harder than gold (150-200HV), the materials currently used for coating test probes.
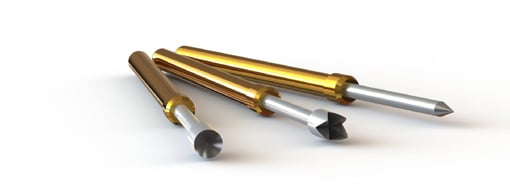
By coating test probes with two different alloys, a sharper, harder tip can be produced while reducing the cost for the probes.
An Ultra MaxPhase coating follows the profile of the probe surface without developing the brittleness found in rhodium, producing a perfectly sharp tip without roundness. This allows the use of a tip with a harder and sharper profile than is possible with either gold or rhodium, enabling forceful, accurate application as well as precise piercing action, for instance to penetrate cable insulation.
Cost efficient test probes To optimize electrical conductivity between the plunger and the barrel of the test probe, the plunger sides are coated with a different alloy, Silver MaxPhase™. The material offers the same electrical conductivity and wear resistance as gold, but at a much lower cost. Ultra MaxPhase and Silver MaxPhase are applied to the test probe using PVD (physical vapor deposition). The technique allows coating of the two alloys in the same production process for more versatile and cost efficient test probes.
Coating services and turn-key production equipment As well as being costly, gold and rhodium are often subject to volatile price fluctuations, while the alloys used in Impact Coatings’ process have stable prices over time. The coating cost can be reduced by 20-50% compared to rhodium or gold, depending on whether the production is outsourced to a coating service or operated in-house. The process has been tested and verified for use on PCB test probes. Impact Coatings provides both coating services of Ultra MaxPhase and Silver MaxPhase and turn-key production equipment for coating on test probes. The coating service is carried out at the company premises in Linköping in south-central Sweden, an area with good communications for transportation worldwide.
.
For further information, please contact Impact Coatings AB Westmansgatan 29 SE-582 16 Linköping, Sweden
Peter Högfeldt, Business Area Manager, Electrical Contacts, Tel:+46 13 35 95 01 Mob: +46 708 87 44 34 [email protected] www.impactcoatings.se