The Moldplas 2015 will be held in Batalha, Portugal from 28 to 31 October 2015. ARBURG will be presenting a complete range of plastic parts production - from one-off parts through to high-volume production - on Stand 3B04, Hall 3. The Freeformer for industrial additive manufacturing will be presented in Portugal for the first time. In the injection moulding area, there will be a demonstration of multi-component injection moulding of iPhone covers.
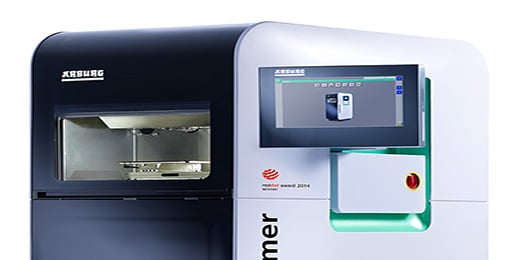
"The Freeformer will enable our customers to produce prototypes in the material of their choice, thereby achieving a significant reduction in development times. Moreover, it is also possible to produce fully functional parts in batches as small as a single unit," says Martín Cayre, Managing Director of Arburg’s Spanish subsidiary.
Freeformer additively processes two components The Moldplas 2015 will be the first time that the Freeformer and Arburg Plastic Freeforming (AKF) will be seen in Portugal. The Freeformer uses the patented "Arburg Plastic Freeforming" process to produce fully functional parts from qualified plastic granulates based on 3D CAD data, without the need for a mould. The granulate is first melted in a plasticising cylinder as with injection moulding. Plastic droplets are then applied layer-by-layer onto a moving part carrier via the nozzle of a stationary discharge unit, using high-frequency piezo technology at a specified duty cycle (60 to 200 Hertz). The second discharge unit can be used for an additional component in order, for example, to produce a part in different colours, with special tactile qualities, or as a hard/soft combination. At the Moldplas, the second component will be used to produce a part with complex geometries using water-soluble supporting structures. Subsequently, the supporting structures are simply removed in a water bath.
Multi-component injection moulding As an example of the automated production of high-volume parts, an electric two-component Allrounder 470 A will be used at the Moldplas 2015 to produce covers for an iPhone 6. This application will be realised with Portuguese partner Plasdan, which will provide a 1+1-cavity mould, special rotation technology and, in addition to the size 290 electric injection unit from Arburg, a second electric injection unit that can be retrofitted to existing machines. The two-colour iPhone covers, made in a hard-soft combination, are produced in a cycle time of 21 seconds. A Multilift Select robotic system is used to handle the moulded parts, which weigh around 15 g.
Alldrive high performance series The Allrounder A has an energy requirement which is up to 50 per cent lower than for standard hydraulic machines. Servo drive energy recovery during braking also contributes to this saving. Short cycle times are achieved with the aid of the standard, servo-electrically driven independent main axes. Play-free, direct-acting spindle drives ensure maximum repeat accuracy and part quality. Low emissions thanks to liquid-cooled, encapsulated servo-electric drives are a further benefit. Convenient operation of the production sequence is ensured by means of the universal Selogica control system.