Arburg was represented at the Euromold for the first time last year, where it impressed trade visitors from the mould construction, design and product development sectors with its newly developed Freeformer. From 25 to 28 November, Arburg will demonstrate the potential of Arburg Plastic Freeforming (AKF) for the industrial additive manufacturing of fully functional plastic parts with two Freeformers at the Euromold 2014 in Hall 11, Stand D25.
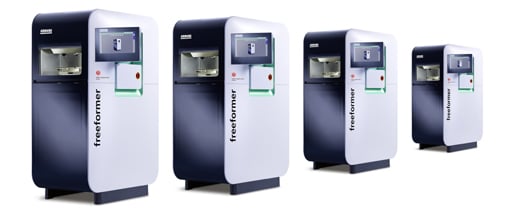
The two Freeformers at the Euromold 2014 will be equipped with a three-axis component carrier and two stationary discharge units. This is the version which has been enquired about by most of the potential customers to date. The exhibits will demonstrate how functional components can be additively manufactured from standard granulate based on 3D CAD data.
Two-component application with supporting structure The second discharge unit can be used for an additional component in order to e.g. produce a part in different colours, with special tactile qualities, or as a hard-soft combination. Brand new for the Freeformer is the option of building up water-soluble structures from a special supporting material. This makes it possible to achieve unusual or complex component geometries. An application of this type will be demonstrated by a Freeformer at the Euromold 2014 based on the example of a spare part made from ABS – in this case a two-part sliding lock which is used in the Allrounder injection moulding machines. The supporting structures can subsequently be removed in a water bath.
New AKF process for broad product range Arburg Plastic Freeforming (AKF) will be explained based on various animations. With AKF, inexpensive, conventional plastic granulates are the base material – one of the advantages compared to other additive manufacturing processes. As with injection moulding, the granulate is first melted in a plasticising cylinder. A stationary discharge unit with a special nozzle then applies the plastic droplets layer-by-layer onto the component carrier using high-frequency piezo technology at a specified duty cycle of 60 to 200 Hertz. Depending on the nozzle used, the diameter of the plastic droplets generated under pressure is between 0.18 and 0.3 millimetres.
Automatic data processing The 3D CAD data for the parts being manufactured (STL files) are processed offline on a PC. A special software generates the necessary manufacturing data via slicing. Once the Freeformer control system has received this data, which determines, e.g. the axis movements, production can begin. Operation is extremely simple, no special programming or processing knowledge is required.
ARBURG GmbH + Co KG Postfach 1109 72286 Lossburg, Germany Tel.: +49 7446 33-3463 Fax: +49 7446 33-3413
In Switzerland ARBURG AG Südstrasse 15 CH-3110 Münsingen Switzerland Tel +41 31 724 23 23 www.arburg.ch
.
.
...brought to you by Eurotec-Online.com