Ever since the launch of its Crawford Swift ‘Powerstir’ CNC Friction Stir Welding (FSW) machines in 2000, PTG Heavy Industries has been acknowledged as a global leader in this innovative means of jointing metals.
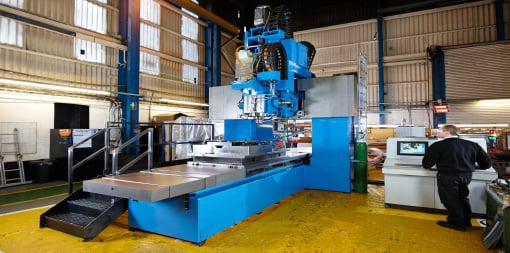
Exotic steel and titanium for aerospace Recent research and development activities at PTG Heavy Industries’ UK-based HQ, however, have taken the capabilities of the welding specialist’s FSW machines further than ever before – to include the successful jointing of exotic steel and titanium alloys that are particularly suited to the uncompromising requirements of space and aerospace applications.
Aerospace-grade titanium of 3mm – 8mm in thickness “We have successfully welded both aerospace-grade steel alloy and aerospace-grade titanium in thicknesses of 3mm and 8mm, using our proprietary PTG fixed pin tooling techniques,” comments PTG Heavy Industries’ Sales Manager, Chris Cheetham.
“Although each presented distinct challenges, including the potential for workpiece distortion and ensuring sufficient heat transfer when blending thicker materials, these issues were overcome.” Comprehensive research programme As part of its research activities, PTG Heavy Industries also achieved excellent results when working with various exotic aluminium alloys ranging from 2mm to 35mm in a number of challenging configurations.
Impressive results with exotic alloys of 40mm in depth “Our successes have been such that we now look forward to applying our findings, approach and technologies to robust testing on other bespoke alloys that are used across the avionics sector,” adds Chris Cheetham. “For example, we have also achieved good results working with exotic alloys of as much as 40mm in depth.
Superior welding for planes and high-speed trains Since their launch, Powerstir Friction Stir Welding (FSW) machines have attracted considerable interest from organisations seeking an innovative way of creating superior high-strength welded joints, without the detrimental and visible effects typically associated with conventional welding.
From small, intricate components to automotive products, aircraft manufacturing, railway carriage panels and shipbuilding, Powerstir Friction Stir Welding provides a clean, highly aesthetic alternative to traditional welding. A method that delivers proven weld quality, FSW offers excellent mechanical properties and virtually no porosity. Patented by TWI (The Welding Institute), Friction Stir Welding is a unique and innovative means of jointing metals. The process combines frictional heat with precisely controlled forging pressure to produce extremely high-strength joints that are virtually defect free. Friction Stir Welding transforms the parent metal from a solid to a plasticised state. This occurs during a process that involves mechanically stirring the materials together to form a high-integrity, full-penetration welded joint.
Incorporating the brands of Binns & Berry, Crawford Swift, Holroyd and Holroyd Precision Components, PTG has established itself at the forefront of high precision machine tool design, build and supply. The PTG range includes heavy duty lathes, deep hole drilling machines, Friction Stir Welding (FSW) machines, ultra precision grinding machines for rotor, thread and gear operations; rotor milling machines and special purpose machine tools for the manufacture of precision components. Industrial sectors served range from aerospace, medical and mould tool & die to marine, power generation, mining, oil & gas, steel, high end and heavy automotive. www.holroyd.com