At the next EMO in Mailand, Tornos will unveil in world première its new loading system on multispindle lathe, the "chucker" in version 2009. This solution allowing customers to work with sintered, casted and forged parts will open widely the spectrum of possible parts machined on a multispindle lathe.
A growing trend In some cases, using the "chucker" solution is far more interesting to machine parts. The sharp increase in the price of materials means that ways to reduce scrap to a minimum are always sought after. The race for profitability is sensitive to the reduction in floor space. For the others it is always possible to work with a "chucker" solution and a bar loader, that way it’s total flexibility to pass from one to the other.
Automated loading Blanks/billets often arrive in a palette close to the machine, then a robot takes the part and load the machine. More and more clients are requesting this solution for the parts they order. The benefit of palettisation is that this operation reduces the number of different handling procedures for each workpiece, whether it be for cleaning and dispatching or even for other types of operations such as thermal treatments, for example. This reduction in human interventions cuts down on the transit time as well as the risk of damaging the workpieces and different costs that this incurs.
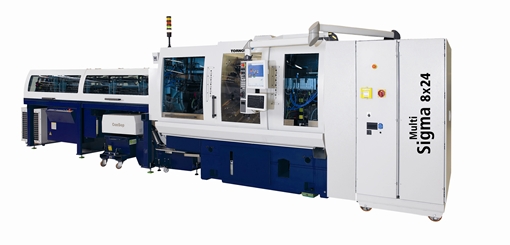
Nothing but benefits It is rare to find solutions which only offer advantages. Indeed, a turning machine designed for the machining of blanks loses none of its initial capacity – in the event of a change of process, for example – when following up with bar work. The machine’s kinematics remain identical, both on the chucker and the bar feeder versions. It is therefore totally feasible to add on a bar feeder without the need to make any significant modifications to the turning machine. This way, bar turners lose none of their initial investment in the turning machine. The opposite is in fact true: they actually win.
In chucker mode, they will actually be able to machine tubes as well as larger diameters because they will have the option of an internal fixture placement. A further benefit – and a considerable one at that – will be in that they will be able to machine workpieces in materials or primary shapes which are unavailable in bars.
Want to know more about these solutions? Do not hesitate to contact Rocco Martoccia at Tornos Phone ++41 32 494 44 44 [email protected] www.tornos.com