Whether a manufacturing company specialises in producing nuts and bolts, complex gear sets or high precision valves, keeping its equipment running efficiently is the key to profitability. Lubrication plays an integral role in reducing friction between critical rotating or moving machine tool components, which can translate into equipment durability and availability.
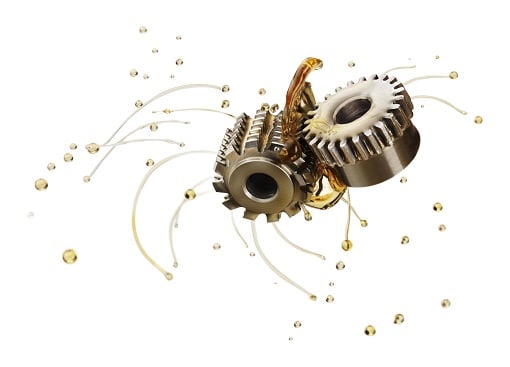
To help ensure that the machine tool runs smoothly, it is important to choose a combination of high-quality lubricants – slideway oils, water soluble cutting fluids and neat cutting oils.
Slideway Oils Poorly formulated slideway oils may not separate readily from aqueous coolants. This can result in the formation of ‘tramp oil’ which can compromise the effectiveness of the coolant by shortening its effective life and adversely altering cutting performance. Tramp oil can also lead to bacterial growth resulting in foul odour, short service life and potential health and safety concerns.
Water Soluble Cutting Fluids To optimise productivity it is very important to choose technology-leading aqueous coolants. The highest performing coolants can provide reduced maintenance requirements by resisting biological attack which helps to extend batch life. Ease of maintenance needs to be balanced with good machining performance as well as protecting the machine tools and work pieces from corrosion and sticky deposits. In addition, the fluids should meet the latest Health and Safety regulations and be easy to monitor and maintain in service. Collectively, these properties will help deliver long service life, excellent cutting performance and reduced maintenance downtime.
Neat Cutting Oils Neat or straight cutting oils are used in applications which are beyond the typical performance profile of aqueous coolants, such as tapping and threading of high alloy steels. Properly formulated products can improve machining in high speed automated machining centres through outstanding cutting performance, reduced tool wear and enhanced surface finish. Maintenance professionals should seek products that: Are light coloured to allow clear visibility of the workpiece Have low misting characteristics to help workplace safety and product usage Are chlorine free to support environmental concerns, while balancing with a high degree of lubricity and machining performance
Maximising Productivity As well as utilising high quality metal working fluids, manufacturing companies should also incorporate an oil and equipment monitoring programme in order to maximise productivity. Oil analysis is a series of tests that help determine the condition of internal parts and in-service lubricants. With this information the useful lives of both equipment and oil can be extended by identifying early warning signs such as contamination and wear, which can help minimise unscheduled maintenance.
You can meet ExxonMobil till the end of the week at EMO, Hall 6, stand H38.
For more information about ExxonMobil’s range of metal working fluids or other Mobil-branded lubricants and services, please contact the ExxonMobil Lubricants Technical Help Desk on [email protected] +420 221 456 426 www.mobilindustrial.com