Time will tell, but increasingly, there is evidence that points to the fact that bar-fed mills could well represent the future of complex, small parts manufacturing. To see this coming paradigm shift, one need only walk the halls of the latest EMO, where a number of major machine tool manufacturers displayed their own, unique offerings of bar-fed milling machines.
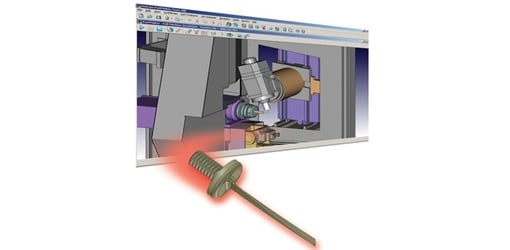
Much as the rise in popularity of multitasking, turn-mill centers and Swiss-type lathes made thousands of manufacturers re-evaluate their programming methodologies, a move to bar-fed milling should cause a similar sort of second look at a company’s approach to CNC programming and CAM software selection and usage. Much like a traditional multitasking turn-mill center, programming a bar-fed mill involves more than simply programming milling in one place and turning in another.
The Function of Bar-Fed Mills As the name implies, a bar-fed mill is a machine tool that, at its heart, is a vertical machining center, with the important exception that a bar-feeder, similar to that found on a production lathe, is used to introduce raw stock into the working environment. The machining table found on a traditional VMC is essentially a second spindle on a bar-fed mill where work can be handed off after being completed on the primary spindle. As a result of this important change in architecture, these machines can achieve the continuous production of a bar-fed turn-mill or Swiss-type lathe, while offering all the machining benefits of a VMC—for example, large tooling carousels and milling horse power.
Turn + Mill ≠ Bar-Fed Milling As bar-fed mills can accommodate both turning and milling operations in a single setup, one shouldn’t make the mistake to assume combining a seat of milling CAM software and two-axis turning software will be sufficient to program these machines efficiently. In reality, bar-fed mills will generally perform turning interspersed with a variety of milling possibilities, from indexing on the face and diameter of the part to polar and cylindrical interpolation. In many cases, even though a part generally starts from round stock on these machines, it may never even see a turning operation, except for perhaps a cut-off operation to transfer the part to the subspindle.
A powerful tool PartMaker CAM software deals with the challenges presented by this range of turning and milling possibilities in two ways. From a toolpath processing perspective, PartMaker employs a "divide and conquer” programming approach, which lets the user break down a part into a series of simpler operations. The programmer can then consider each operation in relation to the coordinate system in which it will occur and the tool motions it will require automatically.
Five-Axis Simultaneous Machining Adding another degree of difficulty for programming bar-fed mills is the ability to perform five-axis positioning and five-axis simultaneous machining. Taking advantage of this capability requires an equally powerful CAM system that supports the virtually limitless programming capabilities five-axis milling introduces.
Simulation To achieve their machining capabilities, bar-fed mills offer some unusual kinematic machine architectures. For example, one common feature of popular offerings of such machines is an "inverted” second spindle, where the work is held vertically, horizontally and degrees in between with respect to the machining spindle, rather than only horizontally as is usual for the second spindle of a traditional turn-mill center or Swiss-type lathe. A CAM system for these machines needs to be able to simulate their unique architectures to allow the user to prove-out the process visually before sending a program to the machine to ensure the setup goes as quickly and efficiently as possible.
For further information on Delcam’s PartMaker software, please contact Peter Dickin, Marketing Manager Direct phone: 0121 683 1081 [email protected]
. Delcam plc Small Heath Business Park, Birmingham, B10 0HJ, UK www.partmaker.com