The integrated electro-discharge dressing technology WireDress® opens up brand new possibilities for grinding with metal-bonded grinding wheels and drastically cuts auxiliary times. According to Fritz Studer AG, it has been possible to increase grinding power in the grinding process by 30% and reduce grinding wheel wear by 70% in comparison with ceramic and resin bonds. Grinding wheels with very intricate con-tours can also be dressed.
. Metal-bonded grinding wheels offer particular benefits when machining difficult-to-machine materials such as high-alloy, hardened steels, tungsten carbides and ceramics. Such wheels offer superior dimensional and thermal stability and dissipate the heat produced by grinding more quickly. The grinding wheels consist of a sintered metal matrix with embedded diamond or CBN grains. They achieve very high removal rates, because the metal bond holds the abrasive grains very well.
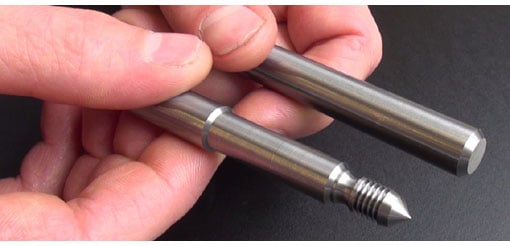
Particularly effective: electro-discharge dressing However, in addition to the advantages of metal bonds there are also disadvantages, as dressing these wheels involves greater expense and effort. Dressing with silicon carbide wheels, for example, often does not achieve satisfactory results, and intricate profiles are not possible. In addition, the grains are difficult to mechanically extract from the metal matrix and are sometimes damaged in the process. It is also not possible to create the high grain protrusion heights necessary to achieve the full efficiency of such grinding wheels. The extremely hard abrasive grains of metal-bonded grinding wheels also lead to heavy wear of the dressing wheels, which results in certain limitations in terms of geometrical precision.
Integrated dressing with wire erosion With Studer-WireDress® Fritz Studer AG brings a brand new dressing device to the market, which uses the wire erosion principle and is completely integrated into the grinding machine and its control system. The grinding wheel never has to be removed for dressing. Thanks to the high proportion of grain space, the wheel is very free cutting. This allows much more grinding oil to enter the grinding slot, enabling a high feed with less workpiece deflection. The dressing intervals can be longer. However, as the dressing process requires so little expense and effort, very complex contours can also be dressed at shorter intervals. As the user can fully utilize the advantages of metal-bonded grinding wheels during rough and fine grinding, the Studer-WireDress® dressing system pays for itself in less than a year.


.
Fritz Studer AG CH-3602 Thun Tel. +41 33 439 11 11 Fax +41 33 439 11 12 [email protected] www.Studer.com
.
...brought to you by Eurotec-Online.com