Precision, reliability and economic efficiency have the highest priority for Buschor Praezisionsmechanik AG. With two Kern Micro five-axis machining centers, the Swiss company has improved its overall performance.
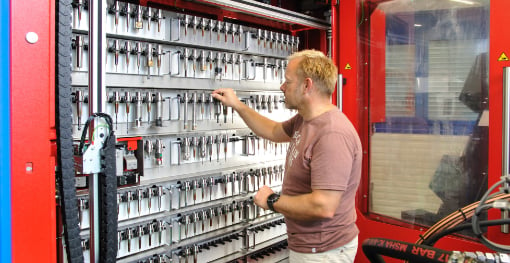
Werner Buschor leaves nothing to chance. In order to manufacture the high-precision parts which he supplies to the optical and aerospace industries, the Swiss medium-sized company has structured the entire machining process chain with incredibly small tolerances. The entire production area is air-conditioned, raw material is always annealed once again before the machining process begins. The manufactured components are checked by Werner Buschor and his team on a high-precision Leitz measuring machine.
Finally, the finished parts are always being directly delivered to the customers - this ensures that they are not damaged during transportation. This whole process underlines the "joy of precision" - which Buschor has also included in his company’s logo.
Werner Buschor has continuously expanded and improved his process chain ever since he founded his company, Buschor Praezisionsmechanik AG, in Au in Eastern Switzerland in 1989. About three years ago, the trained polymechanic needed and also wanted to increase the process reliability of production once again.
Parts with tolerances in the micrometer range were to be produced, automatically and unmanned on night- and weekendshifts. Looking for a machine which could fulfill his needs, he came across the Micro from Kern. After an intensive and inspiring exchange with Kern sales technician Stephan Zeller and visits to Eschenlohe in Upper Bavaria, Germany, he invested in the first machine.
Buschor explains: "The Kern Micro is the first milling center that can stand up to our measuring machine, which we had purchased two years earlier. The measuring machine has a measurement uncertainty of half a thousandth of a millimeter and the Kern Micro offers a positioning accuracy of half a thousandth of a millimeter. The first Kern Micro was immediately connected to a 3R automation system, with the possibility of adding another machine. The large tool magazine with 186 tools and the repeatability of the Kern Micro are ideal for automatic production".
"Finally, we can manufacture workpieces that require the highest precision unmanned", explains the company owner and adds: "Only this way we can secure our profitability at our high-wage location. The empty job market is also forcing us to produce with full automation".
"Since we no longer have to stand at the machine to produce good parts, we have time to take care of the other important things. The other 5-axis milling centers already in place are all automated but do not achieve the necessary process stability in unmanned operation," says Buschor.
"It is a real pleasure to be able to produce high-precision parts with such a machine. When we measure, it’s always amazing to see how precise the machine works."
The thermal stability of the machine is a decisive factor for this high process reliability. Kern sales engineer Stephan Zeller explains: "With our smart cooling management system, we ensure that the temperature of our structural components in our machines remains constant with a max. deviation of 0.2 C."
For the developers at the machine manufacturer in Eschenlohe, Germany, it is very important to install many elements vibration-decoupled or vibration-damped. The patented light-metal axis structure and the Kern software for volumetric compen¬sation bring the performance of this high-tech machine to an unmatched level. Another advantage for Buschor is the compact design of the Kern milling center. According to Buschor, there was not much space left in 2015 when the first Kern Micro arrived: "The ratio of installation area to part size is huge; the Kern Micro allows part sizes of up to 350 mm in diameter with a total weight of 50 kg and achieves this on approx. 4 m2."
It was a surprise for Buschor how much accessibility the machine provides despite of the compact design. “You always have a perfect overview over tools, parts and the whole machining process”, explains Buschor.
For Werner Buschor, the space-saving design has already paid off. When the new orders did not stop coming in, he installed a second Kern Micro in 2017. Now, the tool changer is in between the two machines and provides the tools for both machines. The purchase of a third Micro is already planned.
The high process reliability is not only important in unmanned operation. Since Buschor also manufactures prototypes with batch sizes of only 20 and up to 20,000 units, the two Kern machines are frequently used for these orders. "Especially with complex parts, these parts were always very challenging," says Buschor. They produced a test part, measured it, made corrections, produced another part, measured it and often corrected it again. "With the Kern Micro, the first part already fits, which makes us fast and flexible."
Support is key The entrepreneur’s enthusiasm is also due to the great support KERN Microtechnik GmbH provides. Whenever there are problems, Kern offers outstanding support – for the machine itself as well as for the complete manufacturing process.
One of Kern’s advantages is that Kern has - in addition to the mechanical engineering plant - also its own parts production plant in Murnau, Upper Bavaria. Of course, this plant is well equipped with Kern machines. The technicians working on these machines are always up to date with the latest application technology and are available to assist customers with specific milling tasks.
With his motto, "The joy of precision", Buschor meets like-minded people at Kern. Stephan Zeller, a trained master precision mechanic himself, describes the relation with Buschor: "It makes us very proud that we are able to support the famous ’Swiss precision’ to such a large extent".
In order to provide these services to customers in Switzerland, Kern also has a service location near Zuerich. From the Swiss location, service technicians with know-how and spare parts provide solutions and assistance.