The thermal layout of a mold can be optimized during the design stage, understanding the effect of the cooling channel size and location over the part deformation and its solidification. With Sigmasoft Virtual Molding, which works as a virtual injection molding machine, it is possible to try different concepts and to evaluate the advantage of more expensive approaches, such as conformal cooling, before even starting to cut the steel.
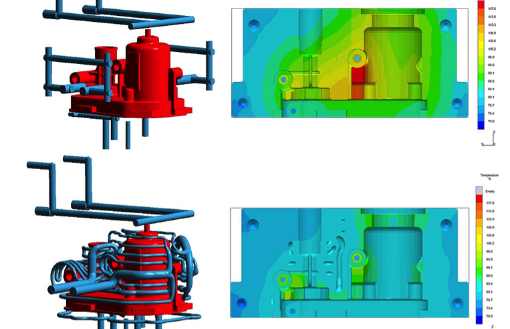
Above: conventional cooling approach and resulting temperature distribution in the mold cavity. Below: conformal cooling approach (courtesy of IPC) and improved temperature distribution.
Thermal mold design is one of the most critical parameters determining the performance of an injection molding operation. Up to now, a lot was left to guessing and prior experiences. This approach is changing with the latest simulation tools, and one of the pioneers has been IPC, Innovation Plasturgie Composites, from Oyonnax, France, who has successfully used Sigmasoft Virtual Molding for six years in the design of their injection molds’ thermal layout.
IPC’s approach has been to carefully analyze the impact of different cooling concepts virtually to find the one that best suits their requirements. The company combines traditional cooling systems with conformal cooling. The analysis performed with Sigmasoft Virtual Molding allows them to quickly detect the impact of every iteration on the mold performance (in terms of cycle time) and on the part quality (regarding warpage and residual stresses).
“Using Sigmasoft Virtual Molding has helped us to be more reliable in the design phase”, states Eric Pauze, Design Manager and Responsible for the Business Unit Conception and Simulation. “IPC has been working on cooling optimization with conformal cooling in ALM in the tools for ten years. We are sensitive to thermal homogeneity of injected parts as a quality criteria check. Each system is designed and then tested using Sigmasoft to qualify the cooling benefit compared to standard systems. Through this software, we had also generated hours saving thanks to the preprocessor efficiency.”
Sigmasoft Virtual Molding follows a unique approach. It works like a virtual injection molding machine, reproducing precisely all the effects seen in reality. The mold, with all its components, is defined in the simulation. Each component is defined with its own material properties. Also the injection molding process is thoroughly set-up, just as in reality. Not only the injection, packing and solidification stages are considered, but also the dead times between processes, which are relevant in the heat transfer of the complete molding cycle.
The part deformation and its solidification behavior are a combination of all factors affecting the thermal mold performance. The thermal layout of the cooling channels is one of these factors. If there is a hot spot in the mold, either due to a very large concentration of plastic material over the part, or due to insufficient mold cooling, the part will shrink more in this area, affecting the overall warpage. A hot spot will also delay the solidification of the part.
In the example seen in Figure , a conventional cooling is considered for a plastic part. The cavity temperature distribution is seen on the right side. Below, the part is optimized with a cooling concept provided by IPC. As seen, the mold temperature is substantially reduced, and the cycle time can be decreased by around 27%.
Sigma Engineering GmbH presents its Virtual Molding technology at the upcoming FIP Solution Plastique trade show at booth M14. The show takes place between 13th and 16th June 2017 in Lyon, France.