In our issue number 375, we wrote about Proto Labs, the "Amazon.com" of subcontracting. In this article we emphasized the novelty of this service largely based on the web and embedded intelligence of "supercomputers" of the company to respond very quickly to all solicitations. We also introduced the "virtual and dehumanized" aspects that some clients could feel. About a year has passed and we met with Mr. Bernard Faure, responsible for France, Switzerland and Belgium as well as Richard Vaughan European marketing responsible to see the evolution of the company and the perceptions of users and potential. [1].
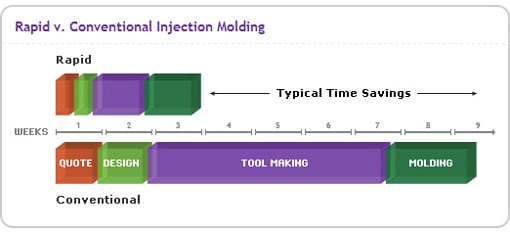
The company is specialized in the realization of prototypes and small series by milling and injection molding with very short deadlines and in "good material". Proto Labs has three production centers, one in the US, one in Japan and one in England to serve Europe.
Reactivity as competitive asset If customers are less accustomed to order online in Europe than in the US, the benefits in terms of speed and flexibility are so high that Proto Labs’s business thrives well. Mr Faure says: "The decision to work with Proto Labs is generally taken under the pressure of deadlines and often our customers start with a few parts to challenge us. As the calculations are largely automated and rely on our knowledge base which is complemented every day, the response time is very fast for quotations. In the case of an order everything is already prepared and we can start to produce at once". The reactivity of the company is so high that production’s time corresponds to a standard response time to a request for quotation on the market. Mr. Faure adds: “We are officially announcing a maximum 24-hour response time for quotations, but in the vast majority of cases we respond within hours. Production then requires from 24 hours to three weeks depending on technical possibilities and choices of the customers”.
New staff for the French speaking markets To deal with the growth of its activity in France, Switzerland and Belgium, the company has reinforced its teams, including a Customer Support Engineer specialised in plastics industry who comes from the world of molds design and manufacturing. Bernard Faure adds: "Thanks to the experience of our support engineer and his knowledge of “this world”, French speaking customers of Proto Labs will benefit from advanced technical support directly in French".
Word-of-mouth to the service of the company Once one has tasted Proto Labs services, it becomes very difficult to do without. Indeed the computer system allows customers to validate the design of their parts directly, then the company’s reactivity can help them reduce time to market. M Faure says: “Word-of-mouth is very positive for Proto Labs. It is not uncommon that engineers who change of companies resume working with us with their new company while the former continues to use our services”. The only constraint to spreading this way of doing? The company is forced to overcome the apprehension of the online order and must of course keep its promises in terms of reactivity and quality. Mr. Vaughan concludes: "We are organized to ensure this responsiveness; our deadlines are naturally met, even if they seem extraordinary for the market”.
{{}}
To support activities across Europe, Proto Labs has sales and technical support offices in France and Germany. For more information Proto labs Bernard Faure Savoie-Technolac 18 Allée du Lac St. André 73382 Le Bourget du Lac Cédex France Phone +33 (0) 479 65 46 50 Fax +33 (0) 479 65 46 51 [email protected]
In the UK: [email protected]
First cut – CNC machining: www.firstcut.eu Protomold – Injection: www.protomold.fr