At Euro PM 2015, organized by the European Powder Metallurgy Association (EPMA) in Reims, France, between October 4th and 5th, Sigmasoft Virtual Molding Chief Technical Officer Timo Gebauer will give a presentation describing how the correct viscosity can be calculated for MIM (Metal Injection Molding) feedstocks.
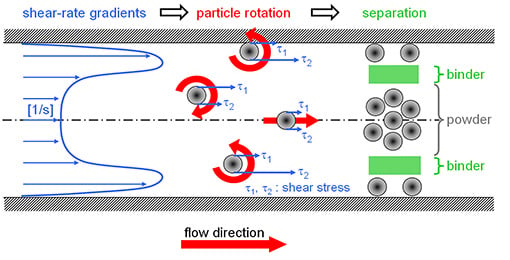
Sigmasoft Virtual Molding is able to predict shear heating and particle segregation, and to couple these effects to predict the real feedstock viscosity. This accurate modelling delivers a better description of the flow behavior and a far more precise pressure demand prediction, a key parameter to determine proper machine size and processing profitability.
Sigmasoft Virtual Molding is already a well-established tool in MIM processes, to predict feedstock molding behavior and its thermal interaction with the mold. To simulate the feedstock flow behavior inside the cavity, viscosity is a key parameter. However, the methods used to characterize viscosity in thermoplastic materials may not be suitable for the characterization of MIM feedstocks.
There is no testing device available to directly measure the viscosity; the values are always calculated indirectly. The most common way to determine the viscosity of polymers at high shear rates is the high pressure capillary rheometer (HCR). The measurements are corrected with theoretical models, but the temperature increase produced by heat dissipation is assumed to be low enough to be neglected. This assumption is accurate enough for thermoplastic materials at low shear rates. However, as the shear rate increases, the heat dissipation due to molecular friction (a phenomenon known as shear heating) starts to be important.
In MIM feedstocks, besides the high shear heating, the rheological behavior can be even more complex, because the shear field leads to particle segregation . Since viscosity is a function of the powder concentration in MIM feedstocks, this segregation leads to significant differences in local viscosity and thus in local flow deformation. “One way to get the right viscosity for a MIM feedstock is to measure it with different particle concentrations. Once the viscosity based on the concentration is known, it is possible to use Sigmasoft Virtual Molding to calculate the correct viscosity”, states Gebauer.