At the Plastpol 2015, to be held from 26 to 29 May in Kielce, Poland, Arburg will present a wide spectrum of plastic parts production – from the manufacture of one-off parts through to the mass production of medical technology items.
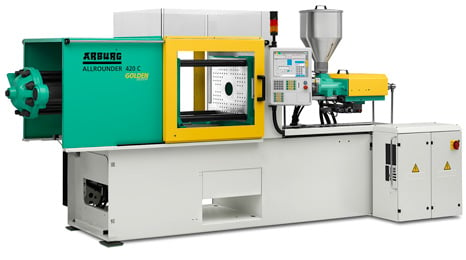
“The Polish economic trend is extremely stable and, accordingly, our assessment of our customers’ willingness to invest is optimistic,” says Dr. Slawomir Sniady, Managing Director of the Arburg subsidiary in Poland. “There’s a particular interest in increasing production efficiency as well as in the competitive production of plastic parts at minimum unit costs. This is precisely what we offer with our wide product range of modular Allrounder injection moulding machines and our reliable service. As a highlight this year, we will also be presenting the Freeformer, which operates without a mould and uses standard granulates to produce functional components as one-off parts or in small batches". Freeformer additively processes two components With the Freeformer, fully functional plastic parts can be additively manufactured from standard granulate using the patented “Arburg Plastic Freeforming” process based on 3D CAD data, without the need for a mould. As with injection moulding, the granulate is initially melted in a plasticising cylinder. Plastic droplets are applied layer-by-layer onto a moving part carrier via the nozzle of a stationary discharge unit, using high-frequency piezo technology at a specified duty cycle of 60 to 200 Hertz. The second discharge unit can be used for an additional component, for example to produce a part in different colours, with special tactile qualities, or as a hard/soft combination. At the Plastpol 2015, a Freeformer will combine a standard ABS material with a special support material to produce a key fob featuring a ball joint. The supporting structures are simply removed later in a water bath.
Hybrid Allrounder produces syringe barrels With the manufacture of syringe barrels featuring a thread, Arburg will demonstrate how disposable items can be produced in high quality and large volumes. Using a mould from Tim Plastik, Turkey, a hybrid Allrounder 520 H with a clamping force of 1,500 kN will produce eight 20 ml syringe barrels from PP in a cycle time of around eleven seconds. The part weight is around 7 grams. Sophisticated temperature control technology is used in order to meet the stringent part tolerance requirements. Before the mould is opened, an unscrewing unit is used to perform so-called Luer Lock thread demoulding.
Hidrive series: combination of electric and hydraulic machine technology The hybrid Allrounder Hidrive series machines are characterised by high productivity, short cycle times and high energy efficiency and are therefore predestined for high-performance applications. The speed and precision associated with electric technology are combined with hydraulic power and dynamics for uncompromising production performance. This is further enhanced by performance-optimised hydraulic accumulator technology. Allrounder H machines bear the Arburg "e²" energy efficiency label as an indication of their energy-optimised operation.
Toy buggy in a single injection moulding cycle Using a toy buggy as an example, Arburg will demonstrate the high-quality, automated and cost-effective manufacture of standard products. This exhibit demonstrates the performance of the proven hydraulic Golden Edition machine series. An Allrounder 420 C Golden Edition with a clamping force of 1,000 kN will produce all the components in a single step using a 1+1+2-cavity family mould. The cycle time is around 30 seconds. After the injection moulding process, a Multilift Select robotic system then removes the sprue as well as the four individual components (roof, chassis and two axles with wheels) and joins them together on the assembly table to produce the finished buggy. The exhibited machine will feature the Arburg productivity package. This package includes the Arburg energy saving system (AES) with variable-speed pump drive and water-cooled drive motor. Here, operation with two control pumps, which enable simultaneous machine movements, is rendered even more cost-effective. Advantages of the productivity package include a reduction in energy requirement by up to 20 percent, five percent shorter dry cycle times and minimised emissions.
Cost-effective entry into automated production The Multilift Select is the entry-level model of the Arburg linear robotic systems. It features servo-electric drive axes and is fully integrated in the Selogica machine control system. For the operator, this means: only one data set, a familiar approach during programming and perfect synchronisation of robotic system and machine. Moreover, the Multilift Select is extremely simple to program thanks to the teach-in function. www.arburg.de