There has been no halt in development at Tornos, where staff are busy working on existing and new products. Even during times of crisis, the company has focussed its attention on the continuing development of its products for the benefit of its customers. Tornos demonstrate this at Siams 2010, where visitors can expect to see an overview of some of the innovations.

Tornos is now making a definitive move into the entry-level segment and thereby covering the entire price segment from simpler models up to sophisticated production machines, but always, of course, remaining true to the company philosophy: high levels of precision and perfect turned parts.
First time in Switzerland This product, which was created in collaboration with Tsugami, is positioned within the entry-level class of Tornos products in terms of price. Of course, the Tornos after-sales department is always available with help and advice for users of this model range too. Even the standard version of the Gamma 20 with its classic kinematics is designed to produce moderately complex turned parts in small to medium-sized production runs. Thanks to the quick changeover options, the machine is ideal for applications in a market where small production runs frequently require a new set-up. The 5-axis version may be equipped with a maximum of 35 tools, of which 15 are driven. The 6-axis version takes up to 39 tools, of which 15 are also driven. In addition, a vast range of attachments and accessories are available for this turning machine.
Total flexibility With the Gamma 20, the user is able to convert work with or without any guide bush within 30 minutes. (sliding headstock and fixed headstock). Thus users can use less expensive bars of material (drawn) and there are not so many large pieces of scrap material, which are also add to costs. There is also the option of working with a synchronised, rotating guide bush, which is of interest in several respects. The guide bush is effectively controlled by an integrated independent motor in the same way as the spindles. It is cooled, lubricated and pressurised to prevent infiltration. This highly efficient principle enables the user to machine workpieces of up to 210 mm in a single clamp setting and without speed constraint, as the integrated motor does not restrict the high performance of the spindle in any way.
At Siams, visitors are also able to discover:
- Micro7 – with gear teeth manufacturing device
- Delta12 – newly equipped with HF spindles
- Deco 20 – counter-spindle 2,3 or 4 jaws chuck
- Almac FB1005 – milling medical parts from bars
- Almac CU1007 – compact machining centre for very precise parts
It is not too late to visit them on Halle 1.1, booth D2/E1 (plan is here).
Today I will gather information about other news to be seen at Siams... tonight you will discover some here!
Cheers py
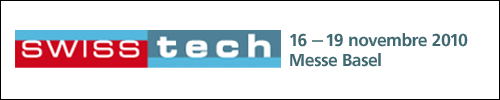