Reflective surfaces made on micro-structures in record time. GF AgieCharmilles is setting a new milestone in Swiss machine building with the model series MIKRON HSM 400, 400U, 500 LP Precision.
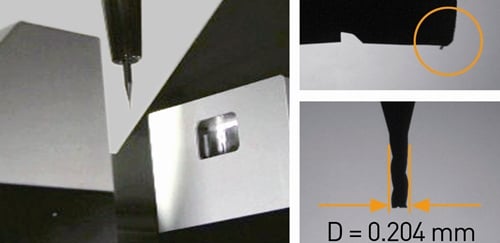
.
GF AgieCharmilles is the only European machine majnufacturer to offer a solution for process-reliable tool measurement on the machine tool. The potential for this functionality was recognized quite early on and thus there began evaluation of intelligent alternatives some years ago. The result is now to marvelled at GF AgieCharmilles: IntelligentToolMeasurement (ITM) - an optical tool measurement at the full spindle speed. “MIKRON HSM LP Precision with its current features is just not practically conceivable without this groundbreaking technology,“ stated GF AgieCharmilles Product Manager Georg Scheiba, who empasized the singificance of this smart machine module.
Precision material cutting operations The MIKRON HSM LP Precision is ushering precision material cutting into a new era. Each of the linear axes as well the rotation/tilt unit has its own cooling circuit. The Opticool concept with its spindle nose cooling also, at the same time, allows a previously unheard of temperature stability. The ingenious cooling management on the MIKRON HSM LP Precision prevents heat flow from the drive motors in the machine bed. This results in a geometric stability which secures the extremely high repeat accuracy in the axial movement management.
Movement is not all What advantages does the user have if a MIKRON HSM LP Precision can perform the smallest axial movements of 100 nanometres (1/10,000 mm) but lack of precision in detection of the tool geometry frustrates achieving this precision class on the workpiece? Everyone who has sought to exactly meet a milled surface again using different tool diameters will understand the practical impossibility of achieving this task. However, this is necessary, in order to ensure perfect crossovers between sections of areas which have been machined using different tools.
A new measuring approach The exclusive tool measurement ITM (IntelligentToolMeasurement) records the whole tool tip up to 12 mm in diameter on modern image sensors. The digitally recorded tool geometry is cleaned up digitally using special software and only then is it measured: thus ITM, for the first time, allows one to obtain a tool measurement with an absolute Z-reference in micrometre range. This is a breakthrough which allows one to develop new and more efficient operating strategies.
An example The basic material to be machined is a high alloy, CrVMo steel (C1.7 Mn0.3 Cr17 Ni- V3 Mo1) manufactured from powdered metal with a hardness of about HRc 60. When removing the average amount of material in a finishing process with a residual oversize of less than 10 μm the whole workpiece surface could be machined to an average roughness of Ra = 0.020 μm = 20 Nanometre = 2 / 100,000 mm. An average roughness of Ra = 0.020 μm represents the ISO roughness class N1. This fantastic result was attained and obtained measured both in the direction of the feed and in the path feed direction.
Mikron Agie Charmilles AG Ipsachstrasse 16 2560 Nidau Switzerland
Tel. +41-(0)32-366 11 11 Fax +41-(0)32-366 11 65