The stainless steel long component sector of the Schmolz and Bickenbach Group of which Ugitech has now become a member is a world leader in the sector, with over 350,000 tonnes delivered in 2008. To remain the leader in this market, Ugitech relies on its research centre based in Ugine (Savoy, France), where 60 people, including around ten engineer, are employed.
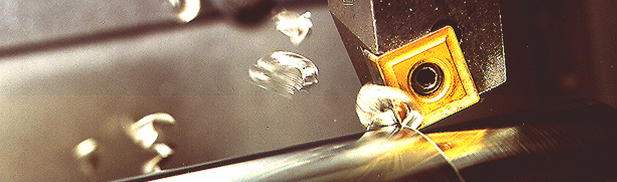
Three types of mission Firstly, the laboratory must be tuned in to the customers needs, understand what they do in order to promote the use of stainless steels and recommend the grade that is best suited to the customer. Secondly, they must develop new products and this is at the heart of the role of Ugitech researchers. Thirdly, they must perfect innovative production processes compatible with a sustainable development policy. Although these three missions are very closely related, in this article we will be concentrating on the first one.
Tuned in to customer needs The research centre has many machines at its disposal for testing machinability. The research centre carries out tests on commercial industrial machines under realistic conditions, measured so as to understand the machining process. In the context of bar turning, a part is created using turning, axial and transverse drilling, sectioning and milling operations. Ugine has recently acquired a Sigma 32 machine from Tornos to carry out these tests.
Results that are immediately put into action Ugitech provides its customers with technical advisors who assist them in getting the best out of the quality of their products: for example, the Ugima product line (stainless steels with enhanced machinability) can increase productivity considerably with Ugitech specialists’ expertise in stainless steels and their machinability. The latest generation of Ugima 2 products enabled those customers who chose to make further advances in productivity (an extra 10 to 20%) and at the same time in tool durability (multiplied by 2 to 5 times depending on the case in question).
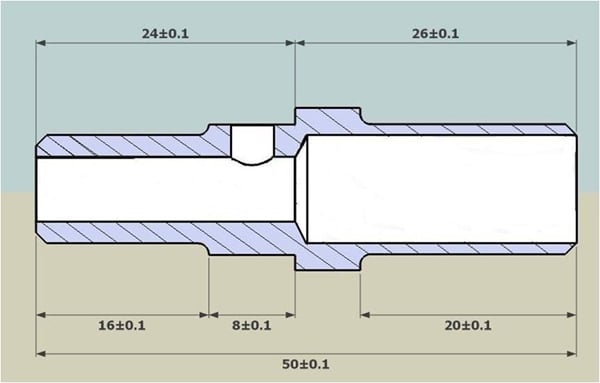
The tests carried out Ugine performs two main types of test. The manufacture of parts in 15mm bar diameter for stainless grades where the parameters are VB15/0.15 < 350m/min. and the machining of a 25mm diameter bar with VB15/0.15 < 350m/min parameters. In both cases, the tests are trying to find the cutting conditions with a carbide coated tool to produce the equivalent of 1,024 parts without changing the tool. The test is repeated three times to confirm the conditions. The tools are monitored constantly. (Speed VB15/0.15: result of the turning tests with an insert reference CNMG120408 and a cut depth of 1.5mm from ray and a feed of 0.25mm/rev. This test involves performing an endurance test where we research the cutting speed that will produce a metal removal rate for the insert of 0.15mm in 15 minutes of machining time. These tests are performed dry.) These tests make it possible to determine or refine the best grades according to their required use.
UGITECH Avenue Paul Girod 73403 UGINE Tel. +33 (0)4 798 938 01 Fax +33 (0)4 798 935 00 [email protected] www.ugitech.com