Whether they are multi-ton steel beams or pins barely visible to the naked eye, magnetized parts can be the grain of sand in the gear and paralyze a production process or be considered defective.
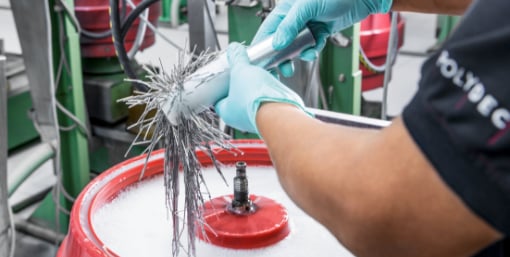
For more than 30 years, Polydec in Biel has been producing precision micro-parts for the automotive and watchmaking industries as well as for electronics and medical technology. Thanks to a machine park of 50 automatic lathes, the company produces about 40 million turned parts per month. Most of them are dashboard axes and injection systems for the automotive industry, an industry that accounts for half of sales. Since the company was founded in 1985, specialists in the Seeland reagion have manufactured more than 6 billion high-precision complex geometry pins, shafts and parts. Some parts produced by Polydec are so small that they are barely visible to the naked eye. But as tiny and numerous as they are, all these parts made of ferromagnetic material are demagnetized, up to four times during the production process. Because one of Polydec’s quality promises is to rid its products of any residual magnetism. This is particularly important for the automotive industry, for which Polydec has obtained ISO/TS 16949 certification.
"Our customers trust us to deliver flawless parts. In the automotive industry, parts are delivered directly to and used in the production line," explains Frédéric Nicolet, the company’s technical director and head of quality assurance.
To meet the high requirements, Polydec uses two demagnetization systems from Maurer Magnetic in Grüningen. Frédéric Nicolet bought the first of the two installations more than ten years ago, the second a few months ago.
"At first, the operation was carried out with a demagnetization coil. The parts were slowly pulled by hand through the coil into an aluminum container," explains Frédéric Nicolet. "The process was very time-consuming and we had to hire an additional person who did nothing else from morning to night. In the end, the parts were not properly demagnetized ».
Over time, the quantities produced have increased and the quality of demagnetization has suffered. This is why Polydec has started looking for a better solution. It found it in 2016 with Maurer Magnetic’s brand new technology.
Maurer Magnetic had developed and patented the Maurer Degaussing technology a few years earlier. Frédéric Nicolet and Polydec are among the first to adopt this unique demagnetization process - and the two companies become partners. Especially because Polydec and Maurer Magnetic have a lot in common: both are committed to high quality made in Switzerland and are family-owned SMEs. Despite a limited number of employees, both companies serve the global market with their products.
"I met Mr. Maurer during the Control show in Stuttgart," recalls Frédéric Nicolet. "I told him about our problem. He invited me to go to Grüningen with a crate of our bulk products, where we determined the optimal demagnetization process through discussions and experiments. Maurer Magnetic then built a demagnetization plant for us with its new technology. When Mr. Konrad, our boss, saw the new facility, he said, "This is the best machine I’ve ever seen! It has only one button, and it works," says Frédéric Nicolet laughing. The assessment of Polydec’s CEO is correct: "Since the initial operation of the new plant, all production has been 100% demagnetized".
But why is demagnetization so important? Frédéric Nicolet explains: "Demagnetization is a characteristic of quality. We demagnetize once after turning because the chips can adhere to the machined parts, which would hinder the proper functioning of our high-precision parts. After hardening and polishing, we separate the parts from the polishing stones with a magnet. The result is again a residual magnetism that attracts particles and contaminates the parts. Other operations, controls and washing of bulk parts also have a magnetizing effect. We demagnetize our parts up to four times."
Residual magnetism can also cause problems in handling and transport processes. If the parts have not been demagnetized, they may, for example, be bent on the Hugi sorting machine or stick to the measuring rollers. Even in the last step of the process, the control with the optical inspection machine, malfunctions can occur.
Frédéreic Nicolet explains: "Optical inspection is very important to meet our customers’ high quality requirements - because as part of quality assurance, the machine must be able to photograph each part individually and analyze the images“.
But demagnetizing no longer gives him a headache: "It’s going incredibly fast. An employee loads up to twenty boxes of 300,000 parts each on a trolley and demagnetizes them in twenty minutes. With the Maurer Magnetic system, this is not a problem."
A few months ago, Polydec ordered a second demagnetizer from Maurer, the MM VE-4, whose old version had reached its capacity limits due to Polydec’s high production figures. "As soon as it had to demagnetize too many crates too quickly one after the other, it overheated," explains F. Nicolet. "Moreover, there is a risk of working with only one demagnetization system: if it fails for any reason, our entire production stops. »
Albert Maurer, Director of Maurer Magnetic, explains how the Maurer Degaussing process works: "Polydec needs very high field strengths for demagnetization because its products are ferromagnetic components made of alloyed or bulk hardened steel. A coil in continuous operation, such as the one initially used, is far from reaching such field strengths. Maurer Degaussing technology operates with a strong and precisely controlled pulse. The short pulse cycle, in the order of a few seconds, avoids unnecessary heating of the coil and saves an incredible amount of energy for high-performance demagnetization thanks to the FMT Field-Multiplicator-Technology technology we use“.
Thanks to the pulse demagnetization process with FMT combined with high-performance capacitors, this design of the MM VE-4 demagnetization system achieves a very high field strength of 305 kA/m. Air cooling with radial fans increases the cycle time, which is generally 10 to 30 seconds.
Mr. Maurer adds: "The pulse allows demagnetization in a few seconds without having to move the part. This method gives very accurate results with a negligible error rate. The impulse reduces energy consumption and costs. There are also fewer staff to employ."
Frédéric Nicolet is satisfied: "This machine is a gift: we were able to save a full-time job and our parts are perfectly demagnetized".