Subcontracted machining - and more particularly bar turning - is a difficult field in which margins are low and the environment very competitive. To succeed in the long term, a company cannot simply offer quality at attractive prices. More and more often, customers are also demanding flexibility on volumes and deadlines, as well as additional services. The French SME JCM Décolletage is fighting on this field and the success is there - attributable, among other things, to the MS 40C multispindle lathes from INDEX, of which it now owns two copies.
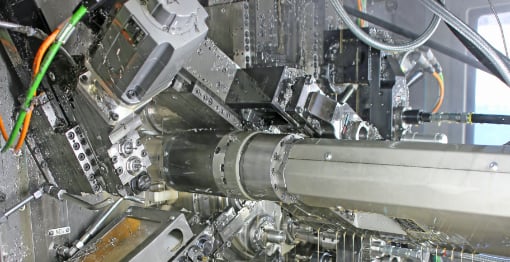
"We started as a traditional bar turning company and have now become a machining specialist offering a very wide range of services and dedicating a large part of its activity to service," explains Michel Jiguet-Covex, owner and manager of JCM Décolletage in Sallanches (France). This region, within sight of Mont Blanc, is one of the major centres of French metallurgy. It brings together hundreds of companies located side by side on the banks of the Arve, whether they are specialized workshops or multinationals. The company founded by Mr. Jiguet-Covex in 1979 started out as a manufacturer of series parts on classic but highly productive lathes. These were still cam-type lathes and not CNC machines. The company quickly recognized that the best strategy for the future was to gradually expand the range of technologies and services it offered. Instead of limiting itself to cheap mass-produced parts manufactured according to drawings, it then resolutely chose to position itself as a full service provider and development partner, able to offer its customers the entire process chain they needed. This involved any necessary additional services and assistance in the design of new products. Today, JCM supplies several sectors, from automotive manufacturers to medical device manufacturers, machine manufacturers, aeronautics and aerospace.
A complete package consisting of service.... "Modern products and the process chains they require are increasingly complex. Few companies are able to handle them in full. It is preferable to receive the support of partners," adds David Grandjacques, production manager at JCM Décolletage. He pointed out that JCM has adapted to this type of need and offers its clients the opportunity to be their unique interlocutor for all the necessary services. Increasingly, they include assistance in the development of new products. JCM helps its customers by providing them with the scope of its production know-how through joint discussions on new projects. In addition to the development of prototypes and pre-series, these development services also include the complete study of the manufacturing process. This sometimes even goes so far as to provide in advance for the subsequent takeover of the actual series production by other subcontractors.
...flexibility... "It is also our principle to respond to customer wishes with a flexibility that is rarely found elsewhere," says Mr. Jiguet-Covex. For him, this is also part of the company’s own service philosophy. And this already applies to the response time to requests for quotations. The customer receives - as far as possible on the same day - an initial answer indicating whether the company will actually be able to send him the requested offer. Special cases such as requests to prioritise delivery calls to avoid bottlenecks or the integration of additional orders are usually processed within 48 hours. For larger development projects, there is no a priori time limit. Nevertheless, the client can assume that JCM will get to work as soon as possible. Last but not least, flexibility also concerns materials, dimensions and quantities. Thus, the company not only manufactures almost all metals common in the industry, but also plastics. It is also reactive in terms of series sizes. According to its manager, it takes care of everything, from small series to volumes of several million pieces, thus presenting itself as a one-stop shop for its customer.
...and a wide range of technologies "For the same reason, we have systematically expanded our range of technologies over the years," says D. Grandjacques. This is why the company invests on average around 20% of its turnover in new equipment each year. Currently, production is spread over four departments. The "classic" bar turning workshop, mainly composed of cam-type multispindle machines, was completed in 2013 and 2017 with three CNC multispindle lathes, including two MS40C from INDEX. This equipment allows the concomitant machining on 6 spindles of bars up to 40 mm in diameter. On these machines, tool changes are easier and therefore faster.
Two other departments manufacture complex parts on 26 NC sliding headstock or fixed headstock lathes that perform extremely precise and delicate machining, primarily for the electronics, aeronautics and aerospace industries, but also for medical device manufacturers. The fourth department has six CNC 5-axis machining centres that produce milling parts with edge lengths of up to 200 mm.
JCM also relies on proven partners to carry out heat treatment or surface coating operations. Since the machined materials sometimes have a very high hardness, the company has grinding equipment at its disposal. For productivity reasons, however, it prefers to use turning or milling for hardnesses below 65 HRC. The offer is completed by 100% inspection and assembly services carried out either by manpower or by sophisticated camera and robot systems. JCM has of course set up a high quality system certified ISO 9001, which is based on a multitude of modern measuring devices.
Why did they choose the MS40C from INDEX? "The decision to acquire our first INDEX MS40C was based solely on our desire to win new customers in markets where we were not yet present," says Mr. Jiguet-Covex with a smile. According to him, the company was simply not in a position, with the multispindle cam-type lathes it had been using until then, to produce certain categories of parts that were more complex in terms of geometry and precision. As for the single-spindle lathes at its disposal, they did not hold up in terms of productivity and costs. In addition, this equipment was not very suitable for quick tool changes and thus limited the possibilities of adapting flexibly to sudden changes requested by customers during the order process. This new equipment has enabled Mr. Jiguet-Covex to manufacture more demanding products at competitive costs and to react much more flexibly to requests for small series or sudden fluctuations during the order process. This experience has been very positive, to the point that the company has since acquired a second MS40C. The latter is used, supplemented by a fully automatic control and assembly device, to manufacture a very demanding subassembly for integration into a turbocharger for motor vehicles.
A close partnership with the manufacturer "We decided to buy a second INDEX MS40C machine because our experience with the first and with onsite representatives was positive," concludes Mr. Jiguet-Covex. These experiences date back to 2005 when the company bought an INDEX ABC. The President points out that the service, advice and training provided by the manufacturer have always been satisfactory to him, both in terms of speed of reaction, skills of the employees and the assistance provided. Beyond the usual commercial relations, he adds that he has succeeded in establishing a real development partnership with INDEX, for example when it comes to assessing the feasibility of new operations or developing specific applications. These relationships of trust built over many years have also contributed to its decision to acquire other INDEX equipment: a C100 and recently this second MS40C tower.
The INDEX MS40C CNC multispindle lathe The robust MS40C CNC automatic lathe has a cylinder with six main spindles and up to two extremely fast synchronous swivel spindles, each with up to six tools for machining the rear surfaces. The MS40C can be configured for bars or plots machining with robot or linear manipulator. Ultra-dynamic carriages allow the use of fixed and/or rotating turrets with a maximum of 3 tools, which offers many machining possibilities. It is also possible to perform contour milling, generation cutting or polygon cutting operations. The work area is easily accessible, allowing quick and economical tool changes. The layout of the work area ensures that chips are evacuated, even when there is a large supply of tools. The machine is supplied with the iXpanel - i4.0 ready control system with an 18.5" touch screen and a Siemens S840D Solution Line control.