2022
Blaser, Switzerland - Blaser examines every chip in detail in an innovative series of tests
Motorex, Switzerland - Fluid monitoring pays off in many ways
Motorex, Switzerland - Motorex Fluidlynx: as perceptive as a lynx
2021
Motorex, Switzerland - Lindner goes green with Motorex Magnum UX 550
Motorex, Switzerland - Very easy: The analysis of process fluids with Motorex Easy Monitoring
2020
Motorex, Switzerland - High-End medical technology from A to Z with Motorex
Motorex, Switzerland - More flexibility through performance with Motorex Deco AP
Condat, France - Responsible performance lubricants for the aeronautics sector
Motorex, Switzerland - Safety thanks to Motorex disinfectants
Motorex, Switzerland - Coolant Management: efficient and sustainable into the future
Motorex, Switzerland - Motorex combines performance and sustainability
2019
Motorex, Switzerland - Ahead of its time: Motorex Swisscut Deco AP
Motorex, Switzerland - Quantum leap with Motorex
2018
Motorex, Switzerland - Proof of performance in the talent factory
Motorex, Switzerland - Optimum performance with Swisscool Aero 8200
Motorex, Switzerland - Optimum performance with Swisscool 8000
2017
Motorex, Switzerland - Versatility pays off
Motorex, Switzerland: Spindle Lube Hyperclean: even greater purity thanks to the "Bag-in-box"
Thommen-Furler, Switzerland - Henkel supplies high-impact cutting fluid...
Motorex, Switzerland - Swisscool Magnum UX 550 ...
Motorex, Switzerland - 100 years of success based around the green barrel
Thommen-Furler, Switzerland - Chemical distributor and eco-responsible
Motorex, Switzerland - Five Motorex sprays that have proved their worth in industry
2016
Motorex, Switzerland - Swisscool Magnum UX 550 stays always cool
Thommen-Furler, Switzerland - Cutting oils for the medical field
Motorex, Switzerland - Process safety with the Motorex Spindle line
Thommen-Furler, Switzerland - Condat Neat Green cutting oil
Motorex, Switzerland - The Jura Technology Cluster
Motorex, Switzerland - Motorex unites innovation and tradition

Motorex, Switzerland - The cult of precision in Täby
Motorex, Switzerland - Synergies increase competitiveness
Motorex, Switzerland - Magnum UX 200 SW, never stop selling it
Motorex, Switzerland - Refill it! Motorex Mini Sprays
Motorex, Switzerland - Many discoveries at the Cassida seminar

Motorex, Switzerland - Opera perfetta -perfect on every aspect
Motorex, Switzerland - Heavy parts with ease
Motorex, Switzerland - A solution with record performences
Motorex, Switzerland - Perfect manufacturing solution
Motorex, Switzerland - Precision turned parts, 100% quality controlled

Motorex, Switzerland - Dynamic turbine wheel on TiAl
Motorex, Switzerland - Protector of the timepiece
Motorex, Switzerland - Motorex International Training 2013
Motorex (itp), Switzerland - Precisely measured
Motorex, Switzerland - The tool in a can
Motorex (Easydec), Switzerland - A million times precisely

Motorex, Switzerland - From development to application
Motorex (SWSTech), Switzerland - 3500 kg of swarf and a giant turbine rotor
Motorex (HK Precision Parts), Switzerland - Swiss quality,made in the USA
Motorex, Switzerland - Pigging technology in action
Motorex, Switzerland - More innovation thanks to the "cutting oil" design factor

Motorex (Joseph Vögele), Switzerland - In the factory of all superlatives
ExxonMobil, Germany - Maximising the productivity of plastic component manufacturers
Motorex, Switzerland - A perfect finish: Swiss Zoom Synt
Motorex (Binder Electronic), Switzerland - Direct connection to success
Motorex (Sweden & Martina), Switzerland - 100% Al Dente

Motorex (Boillat Décolletage), Switzerland - Improving efficiency - innovative lubrication practices
Motorex, Switzerland - Tresor PMC (c) was practically made for us!
Motorex (Bacher Medizintechnik), Switzerland - Medical engineering produced with innovation
Motorex, Switzerland - The green revolution: Motorex Tresor PMC (c)
Motorex (UND), Switzerland - Better performance for manufacturing precision turned parts
Motorex, Switzerland - International training camp

Motorex, Switzerland - First hand know-how: medical technology seminar 2009
Motorex (Meag AG), Switzerland - Cooling lubricant monitoring pays off
Motorex, Switzerland -Technology headstart through exchange of experiences
Motorex, Switzerland -Medical production on a multispindle lathe
Blaser, Switzerland -Residue-free implant production
Motorex, Switzerland -Diametrically-opposed requirements
.
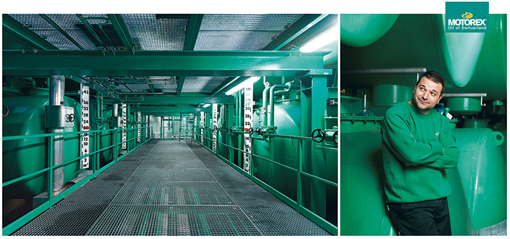