To manufacture injector-holders for common rail systems, a large Chinese automotive subcontractor has acquired the Mikron Multistep XT-200 machining center. With this modular machine the company manufactures various models of injector-holders that require successive complex and highly accurate machining operations.

"For deep hole drilling, we offer a fast, reliable and economic solution to the client based on our solid experience of the interaction between the machine and the tool" says Gerhard Münch, sales engineer at Mikron GmbH Rottweil. To produce no less than three models of injector-holders for diesel common rail injection pumps different machining operations - drilling and milling - are carried out on the blank in hardened steel. Mikron has built a powerful facility specifically adapted to the needs of the customer with three machining cells modules of its design. Each module has two spindles, each with 18 tools located on a tool storage. Special units safely transfer the clamped part from one module to the next one. "With a single clamping we suppress inaccuracies that may occur in the case of multiple clamping and therefore the risks of defects", says Mr. Münch.
60 x d: reliability and repeatability of the process As Mikron always recommends solutions comprising both the machine and the tool, the company had to solve the problem of deep hole drilling with a very small diameter. The main machining operation of injector-holders is a deep hole drilling of extreme accuracy on the whole length of the injector-holders, i.e. 90 mm, with a diameter of 1.5 mm. While one of the parts has a cavity in its center allowing to begin the drilling on both sides, two other parts require a deep hole drilling in a single operation. Münch says: "If 30 x d drilling are already not that easy, the achievement of a 60 x d deep hole drilling comes with extreme requirements." Extremely accurate drilling through the very resistant 42CrMo tempered steel of the injector-holders are an important prerequisite for the proper functioning of the injection nozzles as they will later guide and hold the injection nozzles that are even thinner.
Turnkey solution In total, the production of three models of injector-holders must reach 400,000 a year. Thanks to Mikron Multistep, the automotive subcontractor has integrated the process into its own manufacturing facility. To fully machine the part with all the milling, drilling and deburring operations, the installation requires 50 to 80 seconds depending on the kind of part. If other operations or an extension of the machining steps is required, the installation can be completed by additional machining module and a standard fully automatic loading unit.
Mikron SA Agno Mr. Axel Warth, Head of Marketing and Business Development or, Mr. Boris Sciaroni, Dipl. Ing. HTL / Marketing Manager Phone +41 91 610 61 11 www.mikron.com [email protected] Want to have a look on the Mikron maching solutions? Check out its You Tube channel!
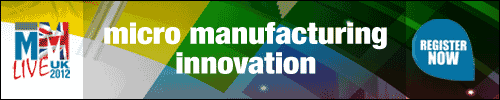