Seals, filters, fluid reservoirs, carriers for special adhesive tapes: Thanks to special material properties, INDUCON brand foams are used in a wide variety of products and industries around the world. Extensive tests in the eurolaser application laboratory have shown that laser systems are far superior to all other cutting technologies in every aspect when it comes to the packaging of materials.
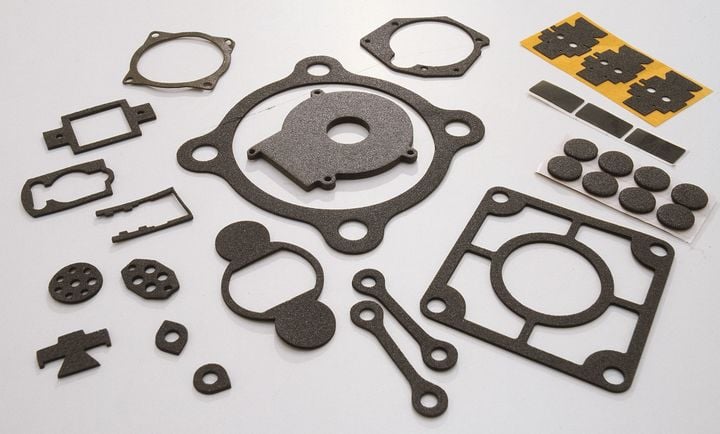
As precise as foam can be processed with traditional technologies, cutting alone rarely gets the job done. CNC milling creates small plastic crumbs that are spread over the work surface or gradually contaminate the tool. Punching machines exert a lot of pressure on the material and often cause material distortion or unclean cut edges. In addition, the production of individual cutting dies is associated with additional costs. Water jet cutting allows the production of filigree structures and precise edges but leaves residues of liquid on the material. Either way, additional quality control or post-processing processes are required after cutting, which are more or less complex depending on the product.
Conventional technology requires post-processing
The extent to which conventionally made-up foam has to be reworked depends not only on the method used but also on the composition and above all on the pore structure of the starting material. Open-cell foams are air- and water-permeable, making them ideally suited for storing liquids. During the assembly in the water jet process, however, the material absorbs moisture along the cut edges and must first be dried before final processing can begin. Closed-cell foams, on the other hand, are usually waterproof, but cutting them to size mechanical means then practically always requires further cleaning processes. Contactless material processing by a laser cutter, on the other hand, not only makes post-processing irrelevant but also meets the highest quality requirements for the use of foam products in sensitive areas.
Foam for safety-relevant products
Mayser GmbH & Co. KG from Lindenberg in the Allgäu is one of the leading providers of such materials. Founded more than two centuries ago as a hat maker and still active as a fashion label, the group of companies now focuses on the areas of safety technology, foam technology, and molded parts production. Foams developed by Mayser can be found in the interior of cars, as sound absorbers in machines and air conditioning systems, or are used to seal measuring instruments and medical devices. The respective workpieces have to meet high quality requirements in some cases, which usually requires additional work steps when assembling with classic cutting processes and ultimately causes higher production costs.
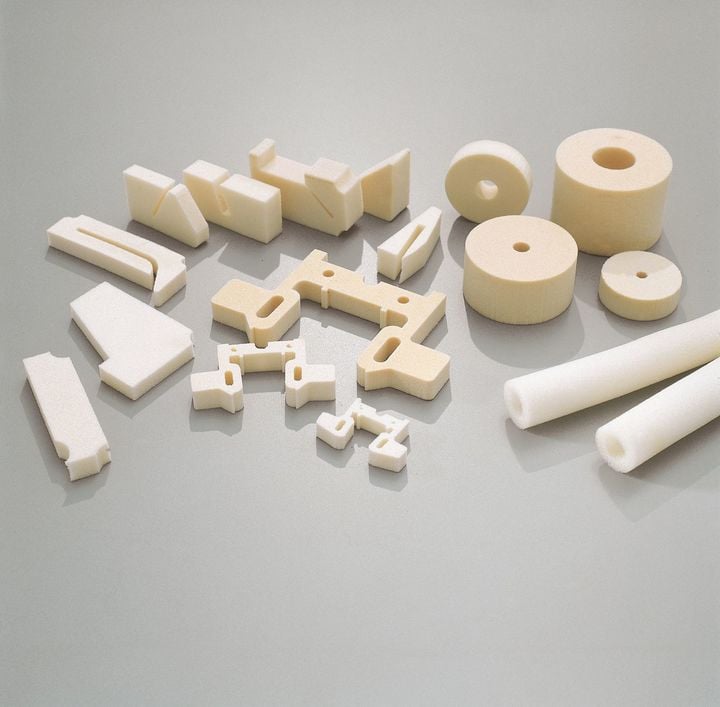
To find out whether laser cutting is also suitable for various foam products of the INDUCON® brand, Mayser commissioned eurolaser to carry out an extensive series of tests. Based on an elastomer made of polyurethane (PUR), INDUCON® products can be equipped with specific properties using various manufacturing processes. As a mixed-cell compression foam, a thermally compressed PUR flexible foam, the material is used to manufacture spacers for machines or vehicles, as an anti-slip covering for office furniture or medical devices. Open-cell products can be used as filters or liquid storage. The common features of all INDUCON® variants include high resistance to chemical substances (including solvents), good insulation properties, and high elasticity.
Modular laser system with maximum flexibility
A system of the type XL-1600 with 400-watt laser power was used for the material tests in the eurolaser application laboratory. The CO2 laser system has a working area of 2,270 x 1,600 mm and reaches processing speeds of up to 1,000 mm / s. With a modular structure, the system can be adapted to individual requirements in almost any way. The link with a conveyor system enables the automatic material feed directly from the roll, which simplifies and accelerates the processing at the same time. With the addition of an optical recognition system, printed material can be cut out fully automatically exactly along the print contour. And if sheet goods are processed predominantly instead of rolls, the efficiency of the laser can be doubled via a shuttle table with two movable tabletops.
INDUCON® is perfectly suited for laser cutting
The laser cutting ability of INDUCON® products was examined on the basis of various tasks, from simple contour cutting to the production of complex geometric shapes. As a result, all tested materials turned out to be “excellently suited” for contactless processing with a laser cutter. After cutting with a eurolaser system of the type XL-1600, the edges did not need to be reworked with other tools, nor was there any waste in the form of lint or dust. The cut edges were neatly sealed during the cutting process.With the test of the INDUCON® materials from Mayser, the advantages of the laser compared to conventional technologies, especially in the manufacture of foams, were once again proven. Foam cut by laser is immediately ready for further processing, the process does not leave any residues on the tool or the work surface and also allows additional steps such as the production of engravings or markings in a single operation. And because completely different materials such as textiles, adhesive films, wood, or plastic can be processed on one and the same laser system without major modifications, laser systems are the perfect alternative to conventional cutting methods, especially for contract manufacturers.